Construction
Stainless steel for high purity applications is our specialty, but for specific needs, Upsilon Process is able to work with super alloys such as Hastelloy, cold or heat-bonded plastics, copper or carbon steel.
#High Purity #SS316L
High Purity applications require the use of a state-of-the-art tooling fleet to meet the demanding needs of our customers. Orbital machines for cutting, grinding and TIG welding are the must haves for carrying out our daily tasks. Upsilon Process has also invested in a Laser welding machine for mechanically welded constructions.
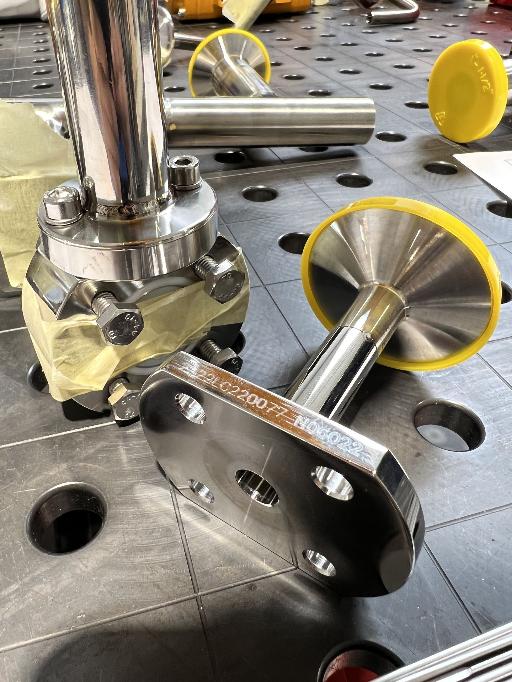
PREFABRICATION
Following the Construction Design and material procurement phases, the prefabrication activity can begin.
PREREQUISITES:
- The project manager and site manager fill out a progress table in which all the isometrics to be produced are included.
- The Validation manager writes a list of qualified welders for the project, which he makes available to these colleagues.
For good execution control, a box number is associated throughout Production with an isometric.
This box is prepared by the site manager (or his assistant) by placing the isometric in question, a blank welding log and all the piping accessories and components to be assembled. Information such as serial numbers, heat numbers and tags are already included on the isometric.
In the end, even before the first pipe cutting, a Quality control is present. The pipefitter only carries out his preparation work and the welder only his welding work. The difference is that the latter must fill out the welding notebook as much as possible at the end of the day.
At the end of the day, all parts - in progress or completed - are returned to their box with the associated documents. The site manager is responsible for checking the overall good execution of his colleagues, before sending the Quality documents to the Validation manager. The progress table is then updated and allows progress on the commissioning phases with non-destructive checks in particular.
Our welders
are qualified
All of our welders are certified by an Notified Body (NoBo) according to ISO14732 and ISO9606-1 standards, including periodic requalifications done internally every 6 months.
In-house welding procedures (WPS) are also certified by an NoBo according to ISO15614-1. These qualified procedures (WPQ) are sent to you in our technical files.
ON-SITE INSTALLATION
The prefabrication stage in our workshops generally follows the installation of the pipes in their final location on the Customer sites.
PREREQUISITES:
- The prefabrication is completed, the assemblies are identified.
- Non-destructive tests for prefabrication welds were successfully carried out.
The installation of the pipe supports is carried out before the assembly of the prefabricated pipes. The inerting of the lines is launched in order to expel the oxygen to a value close to 0ppm. The terminal welds, called assembly welds, are then carried out.
An important stage of non-destructive testing is carried out to definitively validate the quality of our achievements.
If necessary, chemical treatment by recirculation is carried out on site by a specialized subcontractor. If no replacement activity for gaskets and membranes and other polymers is to be carried out, thermal insulation activities can be carried out, once again if the fluid requires it.
This last step brings us to a key point of the project:
Mechanical Completion!
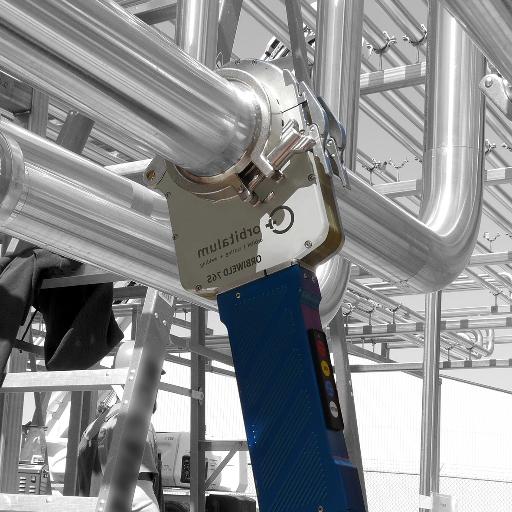