Maintenance
Minimize your OPEX? Maximize your Production? Control your interventions?
Industrial maintenance is a key process to ensure the proper functioning of production equipment in a company. It is a real pillar of industrial productivity. Upsilon Process offers its services for the maintenance of your utilities networks (generation, distribution, storage) and on your production equipment.
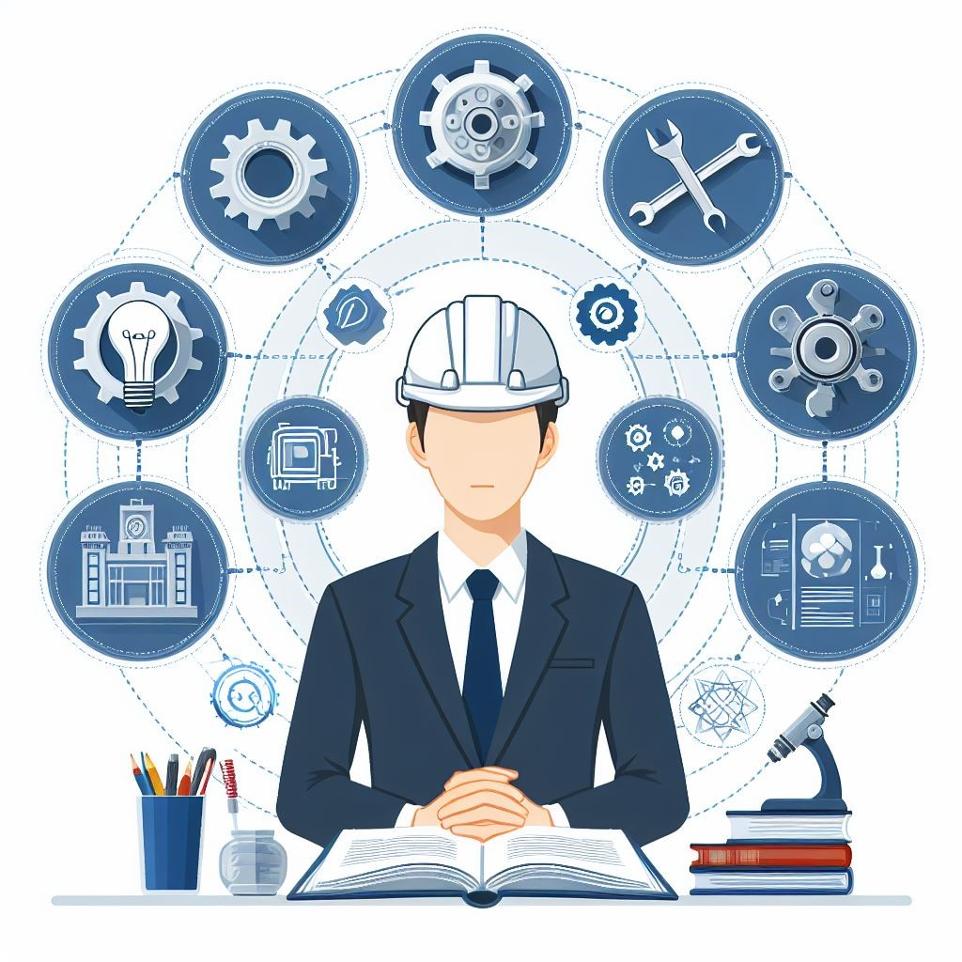
PREVENTIVE MAINTENANCE
Prevention through regular maintenance of an installation, through checks according to standards but also through empiricism.
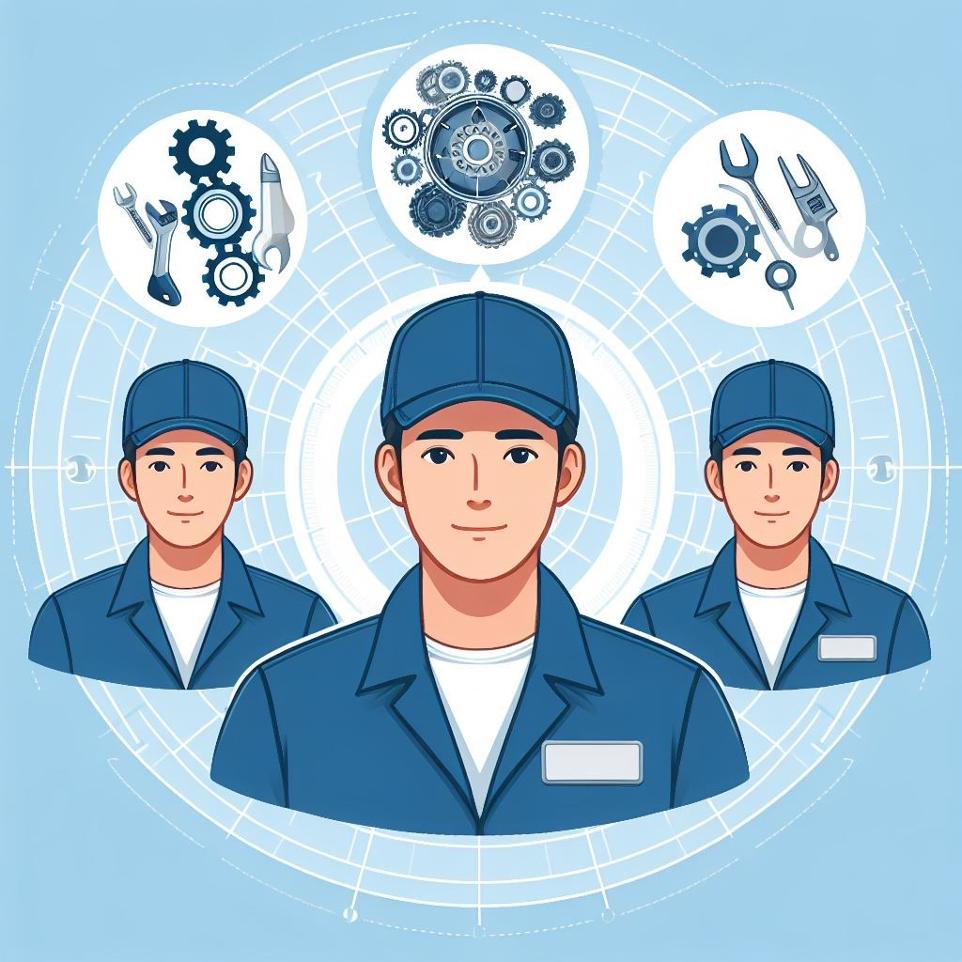
CORRECTIVE MAINTENANCE
Operation undertaken following a breakdown, with the aim of restoring operation through troubleshooting, repair or replacement of defective parts.
DEFINITION
Industrial maintenance is defined in 2001 by the AFNOR (French Association for Standardization) NF-X 60,000 standard, is "the set of all technical, administrative and management actions during the life cycle of an asset, intended to maintain it or restore it to a state in which it can perform the required function."
It therefore encompasses a range of administrative / management / technical actions, including prevention, maintenance, troubleshooting, revision & verification, repair, control & diagnosis of material devices, while aspiring to the improvement of industrial mechanisms .
Costs related to emergency repairs, equipment lifespan, unplanned production downtime and energy costs are each factors that can be influenced by good industrial maintenance management.
ROLE & OBJECTIVES
The place of maintenance is increasingly central to the activity and productivity of companies. Nowadays, maintenance activities no longer only aim to repair equipment but also to anticipate breakdowns and malfunctions. As the saying goes: “Prevention is better than cure!”.
The objectives of maintenance revolve around four main principles:
- Reliability,
- Maintenability,
- Availibility,
- Quality.
The role of a maintenance department is therefore broader today than before, and managers and technicians must integrate numerous parameters such as cost and deadlines, quality, safety and the environment.
PREVENTIVE MAINTENANCE
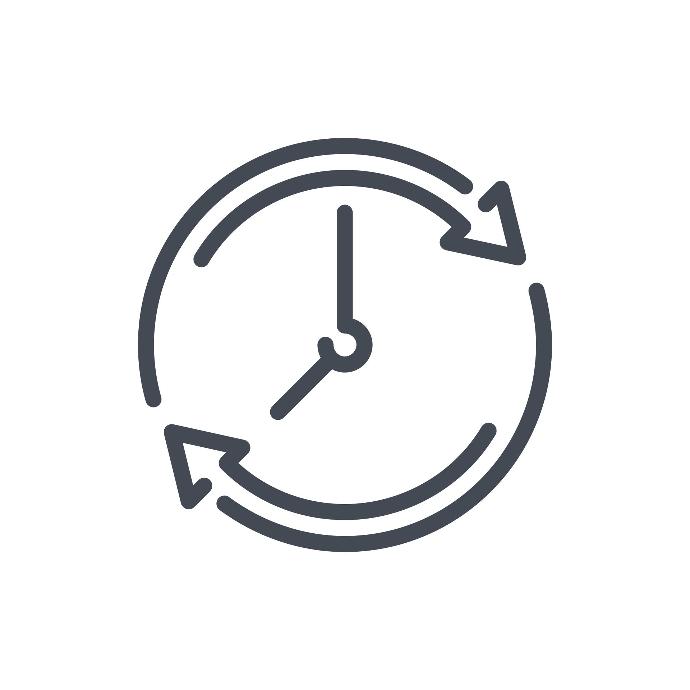
Systematic
Planned and repeatable action.
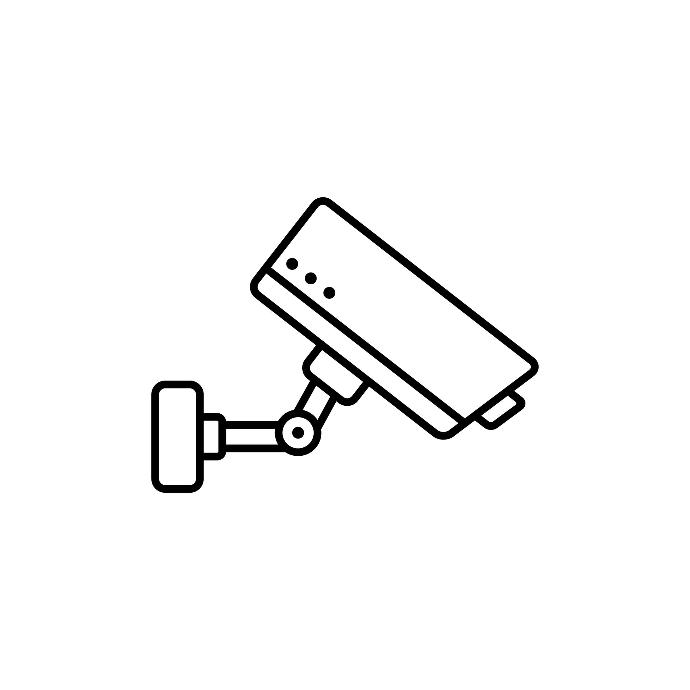
Conditional
Diagnostics by monitoring
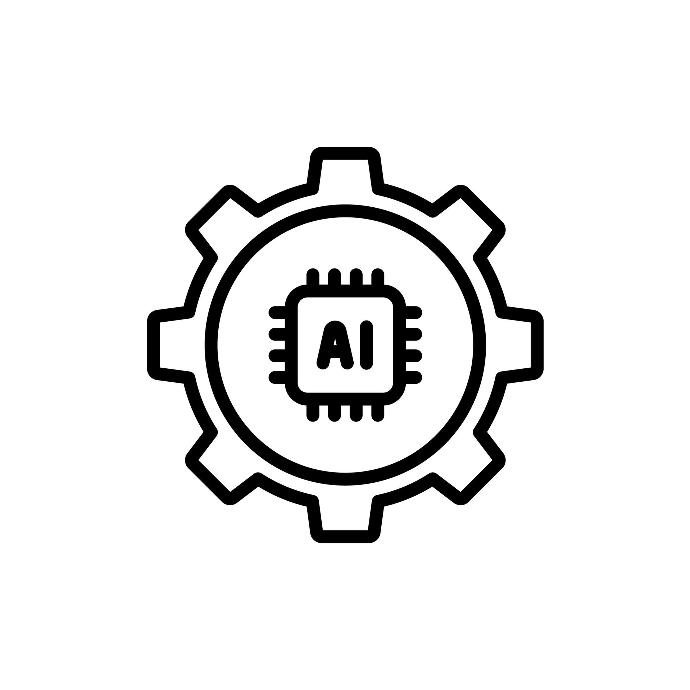
Predictive
Diagnosis by extrapolation
Systematic preventive maintenance is carried out according to a schedule, depending on time or the number of units of use, but without prior inspection of the asset.
The frequency of interventions is established from the start of operation of the equipment or following a partial or complete overhaul of it. It is distinguished by its periodicity.
Its primary purpose is twofold: to minimize the probability of failure and to guarantee constant performance of machines and systems. On the other hand, to be optimal, it must be associated with conditional maintenance so as not to create additional costs, for example.
EXAMPLES OF APPLICATION : Support for the preparation / conditioning of equipment for an AT intervention, support for the start-up of installations, dismantling & replacement of static or dynamic sealing elements, filtration cartridges, control and adjustment of stroke dynamic sealing equipment, adjustment of flow rates of user point valves, I/O control test on control panel (Delta V), resistance and isolation tests of electric motor windings, etc...
Conditional preventive maintenance is based on monitoring of the installation based on a predefined type of event (self-diagnosis, sensor information, etc.). It is characterized by its reactivity to the degradation of equipment.
It uses information collected in real time, using techniques such as visual inspection, vibration monitoring, tribology or infrared thermography, with the aim of intervening at the moment the asset has crossed the wear threshold or deterioration set in advance by the manufacturer.
It’s about carrying out the right operation at the right time, for better cost control.
EXAMPLES OF APPLICATION : Collection of documentary gaps, recommendations based on failure modes & causes, diagnosis and 3D modeling of utility networks, routine inspections with non-destructive testing (NDT) such as thermography on plumbing network valves. steam, tightening torque measurement, etc.
According to the AFNOR definition, predictive maintenance is “conditional maintenance carried out by following the forecasts extrapolated from the analysis and evaluation of significant parameters of the degradation of the asset”.
It consists of anticipating maintenance needs by preventing breakdowns or failures. This is maintenance 4.0, with continuous monitoring of changes in certain parameters, thresholds, different data (CMMS software, etc.), allowing precise management to trigger the right intervention based on all the parameters.
CORRECTIVE MAINTENANCE
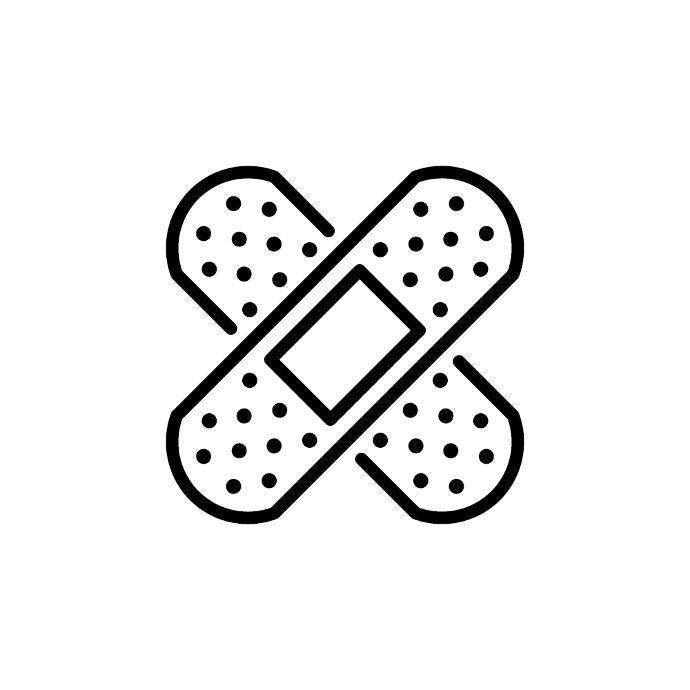
Palliative
Emergency solution.
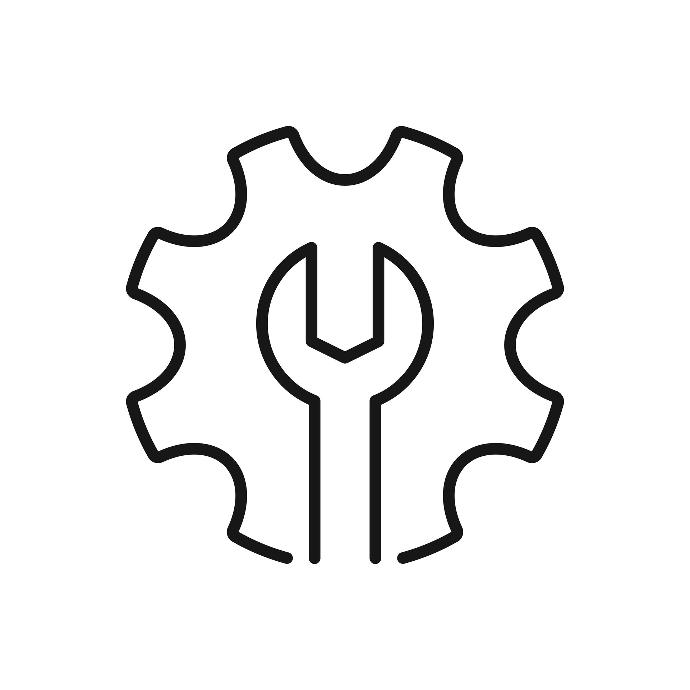
Curative
Identical repair.
Palliative maintenance corresponds to troubleshooting. It consists of temporarily restoring a machine or tool to normal condition, pending its repair. It does not aim to resolve the root cause of the problem. Palliative maintenance makes it possible to avoid a total shutdown of production; we then speak of resumption of production in “degraded” mode. This is a temporary solution!
This solution is used as an emergency measure to avoid business risk. It gives maintenance teams time to plan a more in-depth and complete intervention, of a curative type.
Repair: Physical actions performed to allow an asset to perform its required function for a limited time until repair is performed.
EXAMPLES OF APPLICATION : it starts from the piece of chewing gum 😆 ... But more seriously, it can be the installation of a hose to direct it to a safe place, the placement of a repair sleeve around a leak in a pipe, etc...
Curative maintenance repairs the causes and consequences of the breakdown. Unlike palliative maintenance, this is an in-depth action that acts over the long term, often by replacing the defective part with a new one. The equipment then resumes normal production.
This is the most widespread and widely used type of industrial maintenance strategy: simple to apply and a perfect complement to preventive maintenance.
Repair: Physical actions performed to restore the required function of a broken asset.
LEVEL OF MAINTENANCE
OUR SERVICES
For the launch of its Maintenance activity in 2024, Upsilon Process will be immediately effective and active with its customers in:
- Corrective Maintenance, Palliative as well as Curative:
- Mainly in the form of a Régie service,
- Or if necessary by providing a qualified technician on site for a period of 3 months, renewable.
- Systematic Preventative Maintenance:
- In the form of a lumpsum price, including the Project Definition phase, with the integration of the Methods division.
- Services during technical shutdowns can also be supplemented by a controlled régie quotation if additional needs are identified.
Upsilon Process has the capacity to offer you the first four levels of maintenance for your preventive and corrective maintenance. Our staff, whether internal or external, will be subject to skills monitoring through our training matrix, including internal and external learning and assessment modules via our partners (training organizations, suppliers equipment).
Based on the commercial development of the new activity, Upsilon Process will develop, via its R&D center, solutions such as visual inspection, thermography or vibration analysis to integrate Conditional Maintenance into its package.